INDUSTRIES
Automotive
Carbide materials, particularly tungsten carbide, play a critical role in the automotive industry. Known for their remarkable hardness, durability, and resistance to wear, carbides are increasingly being utilized to improve the performance, efficiency, and longevity of automotive components. In this article, we’ll explore the various applications of carbide in automotive manufacturing and why it has become an essential material for modern vehicles.
1. Cutting Tools and Machining Components
One of the most common applications of carbide in the automotive industry is in cutting tools and machining components. Carbide’s exceptional hardness and ability to withstand high temperatures make it ideal for precision cutting, grinding, and drilling of automotive parts.
•Engine Components: Carbide tools are used for manufacturing critical engine components like pistons, camshafts, crankshafts, and valve seats. These components require high precision and excellent wear resistance, which carbide offers in abundance.
•Gear Cutting: Carbide is widely used in gear cutting tools because of its ability to maintain sharp edges and resist wear during the high-stress process of shaping gears for transmissions and other drivetrain components.
2. Brake Components
Carbide is also used in brake components, particularly in the production of brake pads and brake discs. The material’s wear resistance is critical for maintaining the performance and safety of braking systems over time.
•Brake Pads: Carbide-infused brake pads can withstand high temperatures and maintain frictional properties even under extreme conditions. This results in better braking efficiency and longer service life.
•Brake Discs: Carbide materials are sometimes applied as coatings to brake discs, increasing their resistance to wear and thermal damage, which helps reduce the likelihood of brake fade and extends the lifespan of the braking system.
3. Engine Valves and Valve Seats
Engine valves and valve seats are subjected to extreme heat, pressure, and friction. Carbide materials are commonly used for these components due to their ability to resist wear and thermal damage.
•Valve Seats: Carbide valve seats are durable and maintain their form under high stress, ensuring proper sealing and efficient combustion.
•Valve Inserts: Carbide inserts are used to enhance the performance and durability of engine valves, allowing them to withstand extreme conditions within the combustion chamber.
4. Turbochargers and Superchargers
Turbochargers and superchargers are designed to force more air into the engine’s combustion chamber, boosting engine power. These components work under extreme heat and pressure conditions, which makes tungsten carbide an ideal material for these applications.
•Turbine Blades: Carbide coatings are often applied to turbine blades in turbochargers to improve their resistance to erosion and wear from high-speed exhaust gases.
•Rotors and Compressors: Carbide is also used in the rotors and compressors of superchargers, where its resistance to wear and high temperatures ensures efficient operation over time.
5. Wear Parts for Transmission and Drivetrain
Transmission and drivetrain components are subject to constant friction and wear as they transmit power from the engine to the wheels. Carbide materials are often used in critical wear parts such as clutch plates, synchronizers, and bearings.
•Clutch Plates and Synchronizers: Carbide inserts in clutch plates and synchronizers improve their ability to withstand friction and heat, ensuring smoother shifting and more reliable performance.
•Bearings and Bushings: Carbide bearings offer reduced friction and increased durability, making them ideal for use in the drivetrain, where they help reduce wear on moving parts.
6. Automotive Cutting and Grinding Tools
Carbide’s hardness also makes it a top choice for cutting and grinding tools used in the manufacturing of automotive components. From precision grinding to the machining of metals like steel and aluminum, carbide tools provide the necessary hardness to produce smooth, accurate finishes.
•Grinding Wheels: Carbide-coated grinding wheels are used to sharpen and finish automotive parts, including engine components, gears, and transmissions.
•Drill Bits and End Mills: Carbide drill bits and end mills are used to create complex geometries in metalworking, essential for producing intricate automotive parts like engine blocks and transmission housings.
7. Exhaust Systems and Catalytic Converters
Exhaust systems and catalytic converters are integral to reducing vehicle emissions and controlling pollution. Carbide is sometimes used in exhaust components because of its ability to withstand high temperatures and resist corrosion.
•Exhaust Valves and Turbo Exhausts: Carbide is used in the exhaust system to prevent corrosion and ensure the system lasts longer under extreme thermal conditions.
•Catalytic Converter Materials: While not used directly in the catalytic reaction, carbide coatings can help protect catalytic converter components from high temperatures and mechanical wear.
8. Automotive Molds and Dies
In the automotive manufacturing process, molds and dies are used to shape components during stamping, casting, and forging. Carbide tools are crucial in the creation of these molds and dies because of their wear resistance, high precision, and ability to withstand heat.
•Die Inserts and Molds: Carbide inserts are used in stamping and molding tools that shape metal sheets, plastic parts, or other materials into automotive components, such as body panels, bumpers, and interior parts.
Conclusion
Carbide, particularly tungsten carbide, is a material that brings significant advantages to the automotive industry. From enhancing the performance of critical components like engine parts, brake systems, and turbochargers to improving the efficiency and durability of manufacturing tools, carbide plays a pivotal role in modern automotive technology.
At Zhuzhou Evergreen Hardmetal Tools Co., Ltd, we specialize in the production of high-quality carbide products for automotive applications. Whether you’re looking for durable cutting tools, wear-resistant components, or precision-engineered parts, our carbide solutions are designed to meet the demands of the automotive industry.
Contact us today to learn more about how our carbide products can improve the performance and longevity of your automotive components.
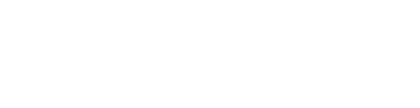
NO.303-4, Plant NO.6, Jin Shan Road 428, Zhuzhou, Hunan, China, 412000
Copyright 2024 Zhuzhou Evergreen Hardmetal Tools Co., Ltd www.300.cn Tags Privacy policy